Toyota Industries Corporation
CN component
We createPOWERcontinuing into the future
Our Carbon Neutral Components contribute to realize sustainable society with powerful, comfortable and friendly POWER to people and the environment.
CN component
Toyota Industries Corporation contributes to carbon neutrality by selling high energy-efficient and low loss electric component and fuel cells.
Engineer interview
Toyota Industries Corporation develops high energy-efficient and low loss electric component. Here are interviews to the developers.
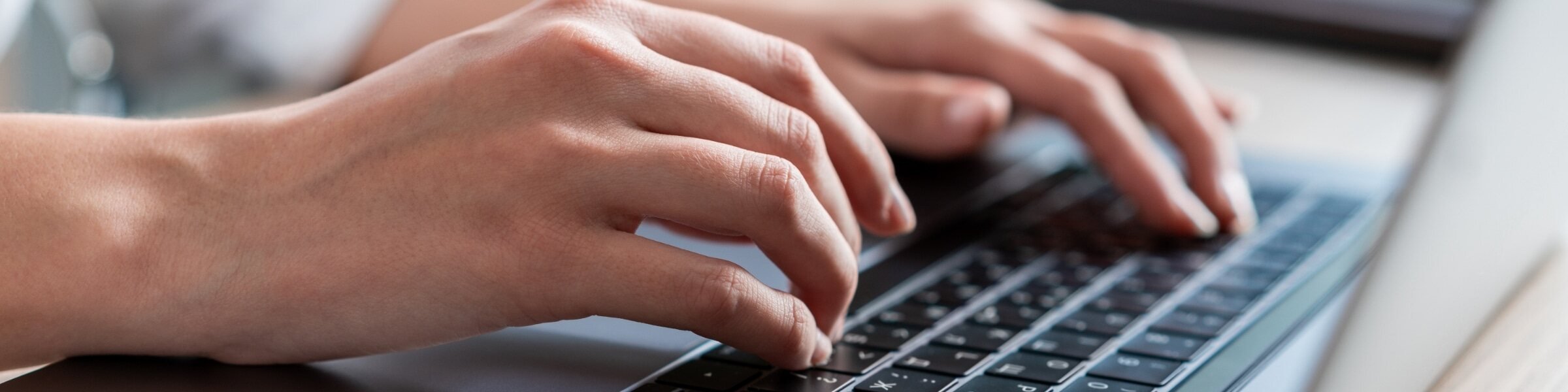
Columns
-
New
Motor
What is Motor Rated Output? (Part 3)-The Relationship Between Motor Cooling and Rated Output
Here is the third column on motor rated output delivered in three parts. The Relationship Between Motor Cooling and Rated Output.
Learn more -
New
FC module
What is a Fuel Cell?
A fuel cell uses hydrogen and oxygen to generate electricity, emitting water. It is seen as a clean energy solution with low impact.
Learn more -
Motor
What is Motor Rated Output? (Part 2) - Understanding Relationship Between Heat Generation, Operating Time, and Rated Output – Keys to Understanding Motors
Here is the second column on motor rated output delivered in three parts. Relationship Between Heat Generation, Operating Time, and Rated Output
Learn more
Blogs
-
2025.07.22New
Carbon Neutrality
Abnormal Weather in June 2025: "Is the Earth Boiling?!"
Record-breaking heatwaves and abnormal weather events occurring one after another around the world are now having a serious impact on our future due to the progression of global warming.
Read more -
2025.06.26
FC Module
Fuel Cell Generators Supporting Future Construction Sites: CSPI-EXPO 2025
Introducing FC power generators that will support the construction sites of the future, exhibited at CSPI-EXPO 2025.
Read more -
2025.06.19
FC Module
【Exhibition Report】Introducing Our Fuel Cell Module at AXIA EXPO 2025!
We exhibited our fuel cell (FC) module at AXIA EXPO 2025. The display attracted significant interest from visitors.
Read more
Catalog center
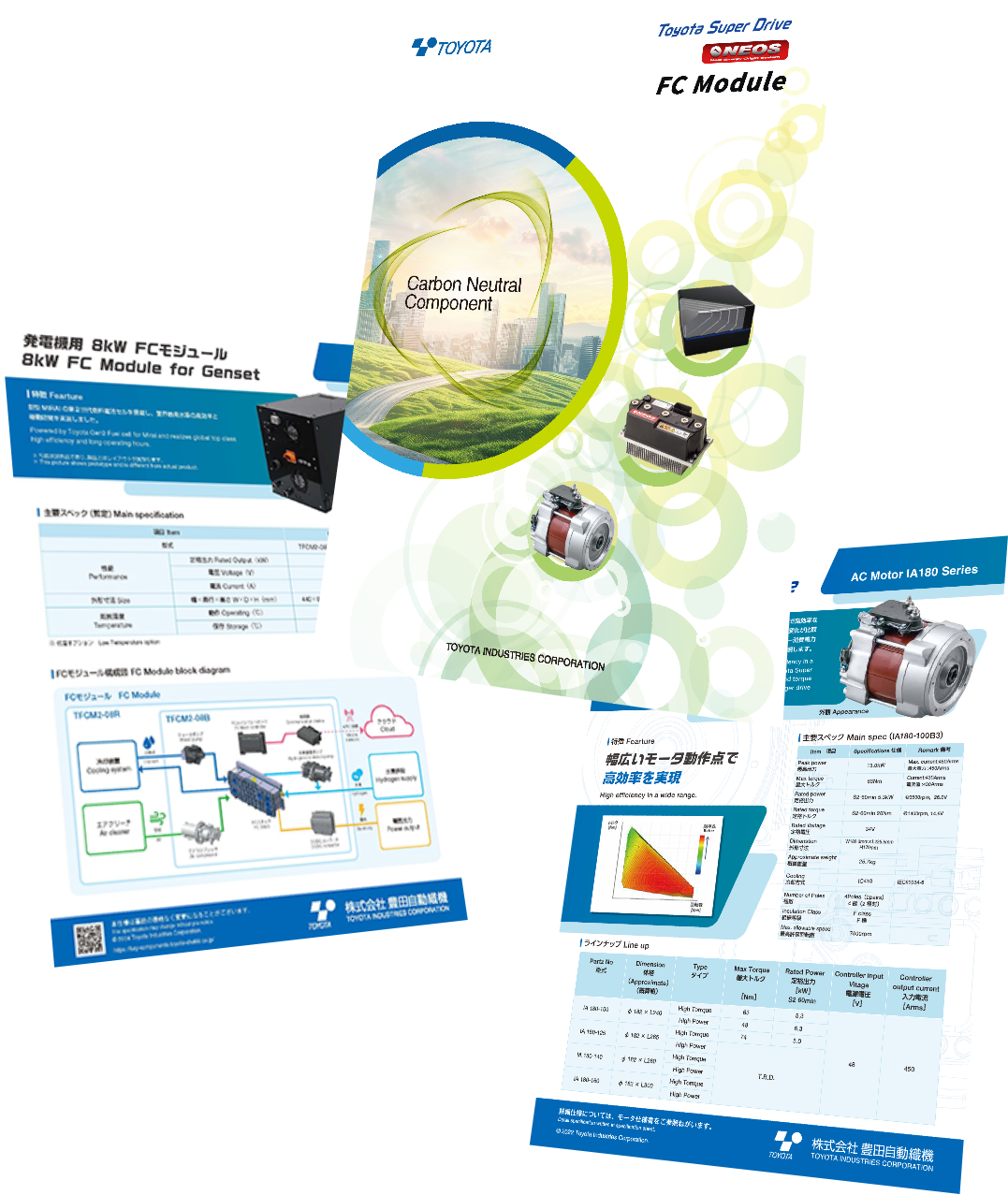
News Releases
-
Exhibit at AXIA EXPO 2025
Toyota Industries Corporation will exhibit at AXIA EXPO 2025, to be held from Wednesday, June 4 to ...
-
Exhibit at FC EXPO 2025
Toyota Industries Corporation will exhibit 8kW FC Module at FC EXPO 2025, to be held from ...
-
Carbon Neutral Component website renewed
We have renewed the Carbon Neutral Components website. We will contribute to achieve net-zero CO2 ...